A small carbon footprint for big climate impact
To show its power in cutting emissions, we share the carbon footprint of our EL 2.1 Electrolyser
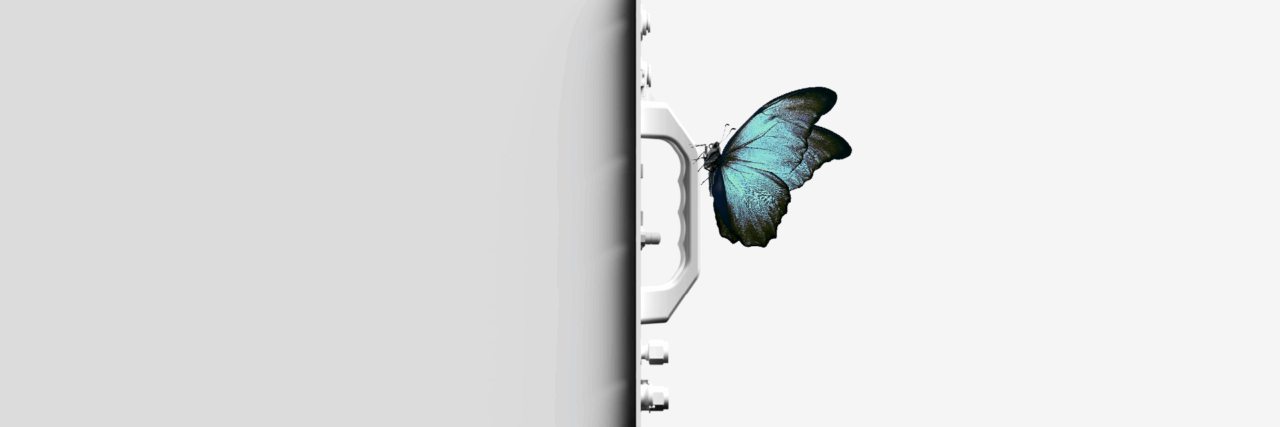
Today it’s crystal clear that green hydrogen is essential for replacing fossil fuels.
Only with this green gas can we fully eliminate the greenhouse gas emissions of fossil fuels across all use cases and flip global warming. But just how big can the decarbonisation impact of green hydrogen really be?
To give the best possible answer, electrolyser manufacturers have to start being transparent about the carbon footprint of green hydrogen generators.
Since transparency is one of our core values, we’re going to start with the EL 2.1 AEM Electrolyser.
Enapter recently ended production of the EL 2.1 and has already begun series manufacturing of our next generation EL 4.0 AEM Electrolysers. So we’re excited both to share the results of our 2021 EL 2.1 carbon footprint analysis below — and to learn and improve on this as we roll out the EL 4.0.
What carbon footprint?
But wait, first, why are we talking about CO2 in green hydrogen? Doesn’t hydrogen production via water electrolysis emit zero carbon emissions when produced with renewable electricity?
Correct. But everything we produce – from the device you’re reading this on to whatever you’re eating or (presumably) wearing – has a carbon footprint. For products, a carbon footprint is the sum of all the greenhouse gases emitted during an object’s creation and its use – and sometimes the period after its use – expressed in kilograms of carbon dioxide equivalent (CO2eq) emissions.
So even though an electrolyser running on renewable electricity doesn’t belch out CO2 emissions, it still has a carbon footprint arising from its creation.
From cradle to gate
What does this look like in practice? Well, CO2-equivalent emissions arise in each step of producing and selling an electrolyser. In 2021, Enapter analysed all of the CO2eq emissions relating to materials sourcing, business travel and manufacturing of an EL 2.1 – a process called Life Cycle Analysis (LCA).
In this early LCA, we tracked greenhouse gas emissions from “cradle to gate”, so from the production and shipping of raw resources to the moment it exits Enapter's production hall.
The cradle-to-gate LCA found the EL 2.1 had a small footprint for huge impact: Just 574 kg of CO2eq.
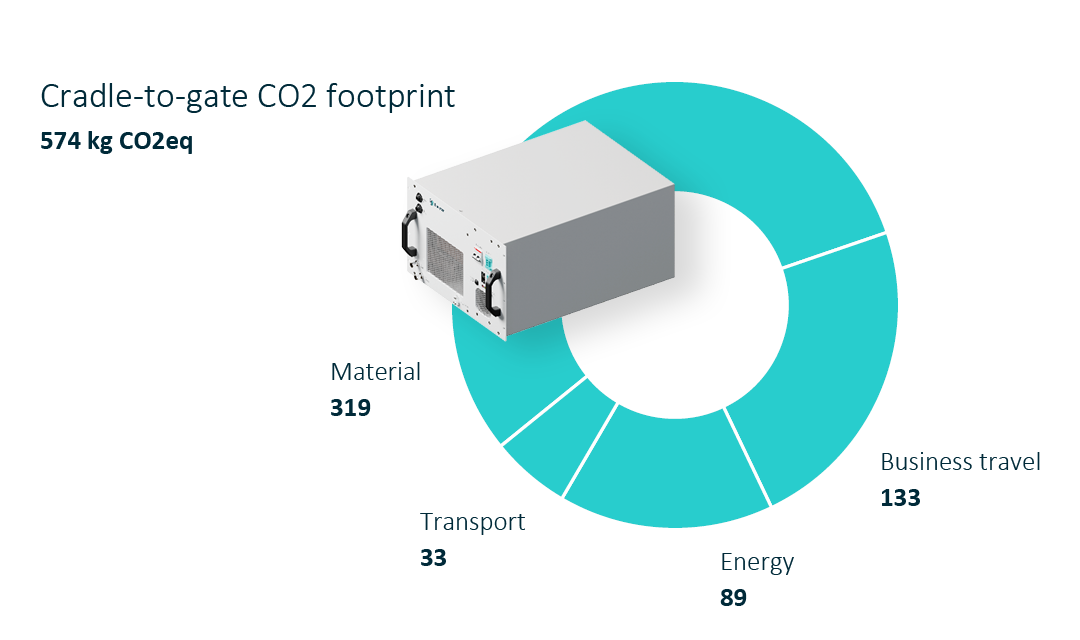
To put that in context, it’s equivalent to about one-eighth of the cradle-to-gate CO2eq of an electric car Li-Ion battery, 29% of the emissions from running an average combustion engine car for a year or just over half of the carbon footprint of an average German’s annual meat consumption.
But no matter how interesting such comparisons may be, they don’t tell the full story – the fact that the EL 2.1 in use has an absolutely tiny footprint compared to fossil fuel use. But how can we tell?
The Fossil Fuel Fighter
To compare the EL 2.1’s footprint to fossil fuel use, we also have to include the carbon-equivalent footprint of the wind or solar devices powering the electrolyser.
Based on a mix of renewable energies from both sources, we’ve assumed a footprint of 1582 kg from the construction of these devices. That takes us to 2156 kg for the entire lifetime emissions of the electrolyser – from construction to all of the power it needs. Which is still tiny next to fossil fuels.
For a start, let’s compare apples with apples... Or, hydrogen with hydrogen:
The CO2eq from producing green hydrogen with the EL 2.1 is 86-93% less than the emissions released in making the equivalent H2 from gas, hard coal or lignite (all data from Umwelt Bundesamt).
There are similar figures for electricity generation using green hydrogen and a fuel cell – the CO2eq is between 89.4-93% less than CO2 from electricity generation with gas, hard coal, diesel or lignite.
And if we look at how far a hydrogen truck could go when fuelled by an EL 2.1 over its lifetime?
The first H2 trucks achieve 400 km of range per tank. Next to a diesel truck, the H2 truck supplied by the EL 2.1 would have a 90% smaller lifetime CO2 footprint, saving 320 kg of CO2eq over that 400km. Assuming 1,000,000 km driven over the life of an H2 truck, that’s over 800,000 kg of CO2 avoided!
Future Footprints
The impact is pretty clear when looking at these numbers. But it’s also interesting to note that the analysis was based on 2020 data – and Enapter’s electrolyser production has since scaled massively.
This means that even if CO2eq arising from sources like our business travel or administration operations may have changed since then, it would have been spread over a much larger number of electrolysers in 2021, and so we believe the real footprint of the EL 2.1 has likely already decreased.
And now we’re moving to the AEM Electrolyser 4.0, where we’ll see this effect even more.
This one-size-fits-all green hydrogen generator is designed for mass production and is part of our concept of zero-negative-impact industrial production: Life Cycle Impact Zero.
The road to Zero
While Life Cycle Impact Zero isn’t just about CO2 emissions, this plays a huge and overlapping part:
For example, all parts of the new EL 4.0 have been designed for recyclability – a circular economy approach aimed at cutting waste and greenhouse gas emissions by decreasing use of raw materials.
The EL 4.0 is also smaller and lighter, also meaning that less raw material input is needed. We’ll continue measuring and improving on its footprint as we roll it out and prepare for mass production.
Carrying out such LCAs is important for our development as it allows us to calculate where we can improve. But equally, it lets us measure the environmental benefit of green hydrogen production through AEM electrolysis by quantifying the CO2 savings and climate benefits of using our product.
Ultimately, this could give an economic value to the generation of green hydrogen (aside from selling and using the gas itself), but it also provides much-needed assurance in an age of misinformation.
As green H2 has gained in popularity and importance, there has been progress towards standardised methodology to calculate its CO2 footprint – and certifications for this to label truly clean hydrogen. We’re fully on board: Our first LCA was calculated internally in collaboration with the Trier University of Applied Sciences and we’re already collaborating with external professionals for the EL 4.0 LCA.
But even now, one thing’s already clear: green hydrogen generation, as demonstrated with the EL 2.1, is a vast improvement on fossil fuel use. Enapter expects the EL 4.0 to be even better.
And we don’t have to wait for this impact – green hydrogen can deliver it right now.
---
Want to learn how the EL 4.0 could unlock your green H2 project? Write to us at info@enapter.com